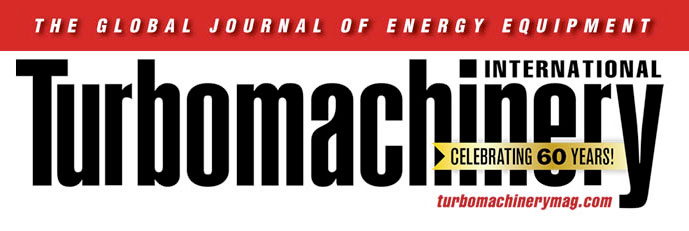
Correct component selection can overcome problems in the functioning of liquid fuel systems in dual-fuel gas turbines. Using the appropriate liquid fuel, purge air and water injection check valves will provide more than 95% availability and reliability — which is far better than the typical 35% – 40% in most dual-fuel applications.
Ensuring Fail Safe
Over the past 30 years, utilities have paid millions of dollars in additional cost when purchasing turbines that have dual-fuel capability or the ability to operate on both natural gas and liquid fuel. While a wide variety of devices have been tried over the years, until fairly recently, technology that addresses all of the primary causes of fuel system failures did not exist.
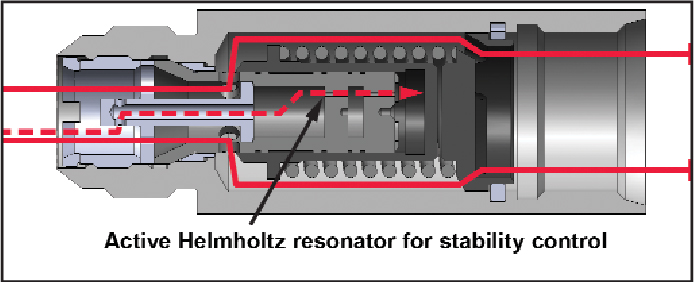
The liquid fuel check valve (Figure 1) is the first component that should be addressed when seeking to improve fuel system reliability. Two key characteristics of the design should be: A Helmholtz resonator and active cooling. These features address the most common failure modes that have been seen over the past couple of decades.
High-frequency oscillation or chatter in the check valve is the result of pulsations from the flow divider which excite the check valve when the resonant frequency of the check valve spring is reached. The reaction of the check valve can be extremely violent.
Hydraulic hammer associated with the rapid opening and closing of the check valve can actually cause the fuel tubing to break. The Helmholtz resonator attenuates the pressure signature of the flow divider output, eliminating the chatter and premature wear of the check valve internals which causes the loss sealing capability. While this design feature has been available for at least 10 years, the stability which ensued after its implementation created an ideal environment for another failure mode — coking.
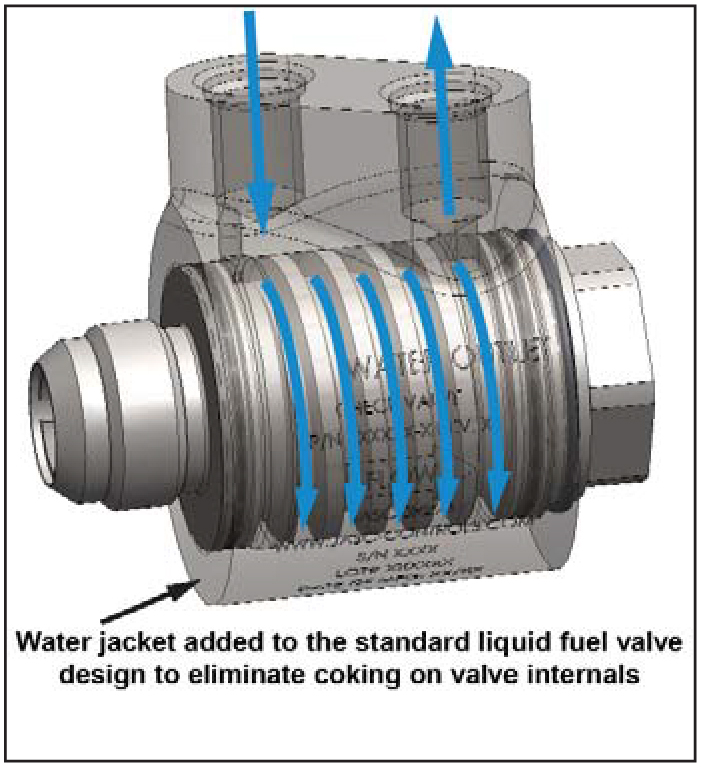
Active cooling (Figure 2) is the next key characteristic required for a liquid-fuel check valve design. Keeping the valve internals below the threshold, which allows the formation of coke, ensures that a Class 6 seal is maintained in the checked and reverse flow direction from hot gas path inspection to hot gas path inspection. The absence of coke formation also enhances the ability to start the turbine on liquid fuel and transfer back and forth between fuels because the check valves are able to maintain the same cracking pressures.
While this technology has only been available since 2005, it has accumulated over two million hours of successful operation in worldwide turbine applications. Specifically, turbines using this technology have demonstrated the ability to service these valves at hot gas path inspections.
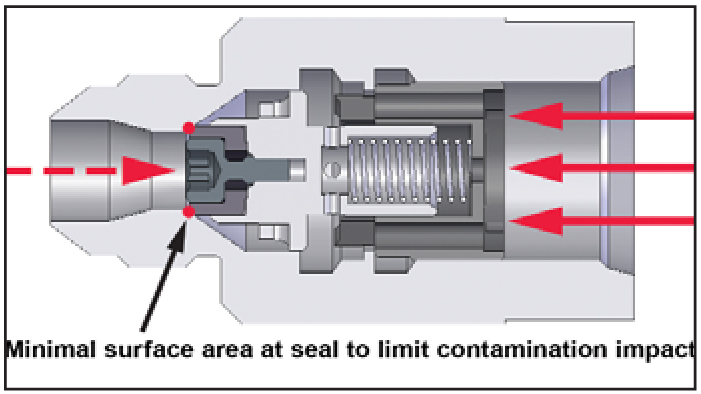
The purge air check valve (Figure 3) is the second component, which should
be addressed. The design should be contamination tolerant, chatter resistant and provide a Class 6 seal in the reverse flow direction. Given the low force margin (less than 1 psi) required for opening the valve, the check valve design should incorporate a knife edge seat to improve its tolerance to contamination.
The purge air check valve design should also provide a toggle action when opening and closing. This feature prevents the check valve from experiencing high frequency oscillation and premature wear of the valve internals. Vibration of the turbine during operation coupled with the low force of the purge air system also dictates that a toggle action design be used. The absence of wear due to chatter ensures that the valve will be capable of sealing against fuel oil in the reverse flow direction when the turbine is operating on liquid fuel.
The third and final component is the water injection check valve. It also has to be impervious to high-frequency oscillations, and capable of providing a Class 6 seal. Otherwise, the pressure signature of the positive displacement pump that supplies the water acts upon the resonant frequency of the valve spring and will cause premature wear of the valve internals when chattering occurs. Maintaining the Class 6 seal prevents the water system from evacuating during periods of inactivity. Consequently, when the water injection system is activated, all of the water lines will be full. This in turn will prevent exhaust temperature spreads that tend to trip the turbine.
In conclusion, implementation of water-cooled, liquid-fuel check valves, purge air check valves and water injection check valves can provide advantages for owners of dual-fuel gas turbines.
Author
Schuyler McElrath, a GE veteran of 22 years, is a consultant for JASC: Jansen’s Aircraft Systems Controls. JASC specializes in the development of new technology for process control problems in industrial, aerospace and aviation applications. Reach McElrath at engineering@jasc-controls.com