This article originally appeared in the Second Quarter, 2010, Combined Cycle Journal Online.
Will your dual-fuel gas turbine (GT) start on distillate the next time you hit the button? Will your engine transfer to oil from gas without tripping offline the next time you switch fuels?
Good questions that many operations personnel would like to answer with a positive “yes,” but can’t. There are several reasons why plants often experience poor reliability on liquid-fuel starts and on fuel transfers, including these:
- Ineffective procedures for assuring high availability of the liquid-fuel system. Diligent maintenance and regular “exercise” of all system components are particularly important.
- Inadequate training of O&M personnel. Liquid-fuel systems cannot be an afterthought; they command respect.
- Off-spec fuel, either through purchase or deterioration in storage.
- Coking of oil in piping and valves located close to hot engine parts.
- Check valves do not reseat properly.
First three items are well within the plant’s control. A solid dose of commitment is all that’s needed in most cases. The last two also are within the plant’s control—at least for facilities equipped with dual-fuel GE Frame 6, 7, and 9 DLN engines (including F class)—but they require a small investment either in new hardware or modification of existing equipment.
You may recall that the first liquid-fuel systems for dual-fuel DLN engines had separate valves for fuel and purge air (Fig 1). Also, that purge air is supplied continuously when the turbine is operating on gas; it is turned off when operating on oil.
Liquid-fuel check valves are prone to coking because of their close proximity to the engines served. Simply put, the light fractions in the small amount of oil that remains in the valve when the unit transfers to gas distills off, leaving a carbonaceous residue which could impede valve operation on ensuing starts and fuel transfers. Residue accumulates with each start and fuel transfer, often preventing proper seating of the check valve when oil firing ends.
When this occurs, purge air and combustion gases can travel all the way back through the oil piping to the flow divider, and beyond, causing fuel system evacuation, corrosion of the flow divider, and other issues. Units experiencing this condition are prone to tripping on the next attempt (1) to start on liquid fuel or (2) to transfer from gas to liquid fuel (no fuel in the line connecting the flow divider to the check valve).
One of the steps undertaken by the OEM to improve the reliability of its dual-fuel DLN frames was to combine the functions of the liquid-fuel and purge-air check valves into one valve body. Today, the three-way purge valve (3WPV) is standard equipment on DLN-equipped Frame 6, 7, and 9 engines (Fig 2). About 5000 of the valves, made by Jansen’s Aircraft Systems Controls Inc (JASC), Tempe, Ariz, are installed worldwide.
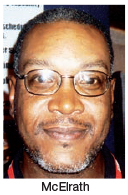
Scores of GTs still are equipped with individual liquid-fuel and purge-air valves and most would benefit from conversion to the 3WPV. However, there’s no stampede, according to Schuyler McElrath, because problems associated with distillate firing have caused many engine owner/operators to just give up on oil. Even the 3WPV is subject to coking problems.
By way of background, McElrath spent nearly 25 years working on fuel systems for the OEM before starting his own company, SMTC Inc, Greenville, SC. He spends much of his time helping users solve liquid-fuel problems on behalf of JASC.
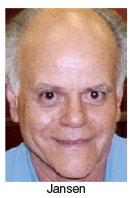
Recognizing the paralyzing effect coking was having on GTs, JASC President Harvey Jansen, a pioneer in high-tech fluid-flow solutions for the aerospace industry, went “all-in” on the company’s ability to develop a “cool” liquid-fuel check valve.
Nearly four years ago, following successful beta tests at a refinery, the company began offering a water-cooled version of the liquid-fuel check valve (WCLFCV). These GE-approved valves now are installed on more than 100 engines worldwide. McElrath reports virtual 100% reliability on starts and fuel transfers.
The next logical step was to develop a water-cooled three-way purge valve (WC3WPV), shown integrated into the liquid-fuel system in Fig 3. A WC3WPV was required because GT owners using this technology needed an inexpensive way to achieve liquid fuel system reliability.
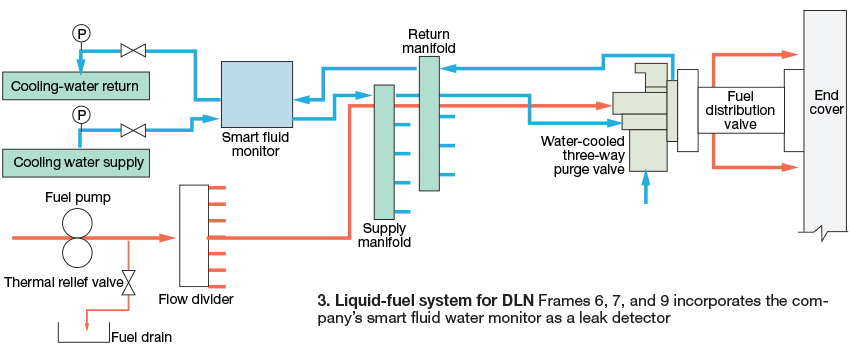
Piece of cake considering the company’s proven success with the WCLFCV. But Jansen, who epotimizes the iconic American technology/business leaders Thomas A Edison and Edwin Land (Polaroid), was concerned more about cost than simply designing a water-cooled valve.
JASC engineers responded with a method for converting existing 3WPVs to water-cooled valves for about one-third the cost of a new valve. Next step was to run validation tests in the lab. The test rig was similar to that used for proof-of-concept tests on the WCLFCV (Fig 4). Photo shows that two uncooled and two water-cooled valves were tested simultaneously.
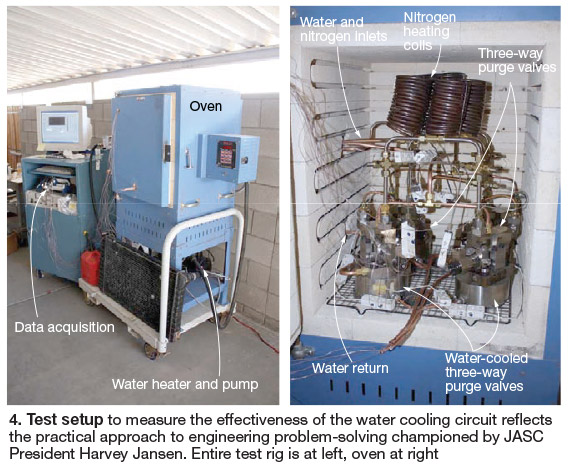
McElrath called in early August to say that the test results detailed in the “Design Verification Test Report” prepared by Project Engineer Kirby Meyer had been accepted by Jansen at the end of July and they proved that the valve was ready for commercial application. The WC3WPV is scheduled for installation on operating engines this fall.
JASC has a rotable pool of valves to swap out with existing 3WPVs—one or two per combustor for a GE frame, depending on the model being upgraded. McElrath says that the valves can be changed out and the water supply and return circuits installed over a weekend.
By contrast, it typically takes about two weeks to convert a turbine outfitted with 3WPVs back to a configuration which uses check valves. The extensive changes that must be made to purge-air and fuel piping are labor intensive.
Lab tests were conducted in an environment far more challenging than the one that exists in a GT package and the results exceeded expectations, McElrath said. For example, the thermal profile of a WC3WPV in Fig 5 reflects purge air at 400F, well above the normal operating service temperature of about 230F.
Note that the purge “air” for testing purposes in the first phase of the testing program actually was nitrogen heated in the coils located at the top of the furnace (right side of Fig 4).
This was done to mitigate any safety concerns associated with a mixture of air and fuel at the auto ignition threshold of diesel oil.
Highest fuel temperature on this run was 292F, the average fuel temperature 240F. The threshold for coke formation is 250F. Regarding the fuel, slightly more than half an ounce (specifically, 20 cc) of No. 2 oil was injected into each of the four valves. Oil was added daily to replenish fuel that had distilled off and was safely vented.
Another test with purge air at 300F, still 70 deg F over normal operating temperature, revealed an average fuel temperature at only 218F. For both runs, the oven temperature was 475F, cooling water 150F (flow rate, 2 gpm).
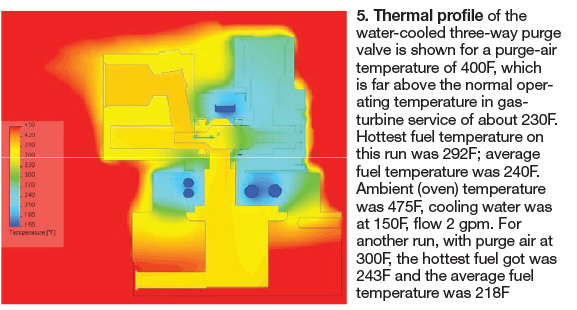
The test program had two major parts:
- A two-day trial with extensive data collection, followed by trending of the data to assure that the test rig would produce the information required to validate (or not) the design of the water-cooled valve.
- A two-week test with about 80 hours of active oven time to assess coking tendency. For this test segment, nitrogen simulation of purge air was shut off and oven temperature increased to 550F to induce as much coking as possible. The two WC3WPVs were monitored continuously to ensure that valve temperature did not exceed 250F. Average temperature of the valves’ spool sections during the two-week run was about 220F.
Over the two-week period, about 6 cc of distillate was added daily to replenish the two 3WPVs, compared to only 1 cc for the water-cooled valves. Consequently, considerable fouling was observed on the spools for the standard valves (right photo in Fig 6); the spools for the water-cooled valves were clean by comparison (left-hand photo).
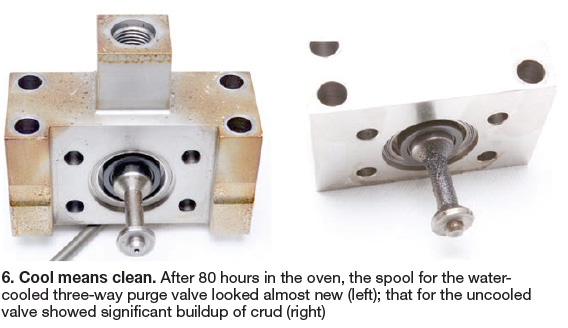
Finally, regarding tightness of WC3WPV shutoff, expectations were surpassed. Better than an ANSI Class VI seal was achieved. More specifically, the WC3WPV spool seal was bubble-tight using 300-psig nitrogen.
To dig deeper into the details of the validation test program for the WC3WPV, access www.jasc-controls.com.